Impression 3D
Comme introduit précédemment, une des technologies qui a récemment connu un grand essor, et qui est le sujet principal de ce livre, est l'impression 3D. Cet outil de fabrication digitale n'est pas neuf, mais ce n'est que récemment qu'il s'est invité dans le foyer des particuliers.
La figure 6 montre mon imprimante 3D, installée à mon domicile, avec une série d'objets qu'elle a imprimé. Et comment fonctionne donc cette imprimante ? En deux mots, du filament chauffé, et donc « fondu », est déposé par une tête d'impression, en suivant un motif très précis, couche par couche, faisant ainsi apparaitre l'objet 3D petit à petit.
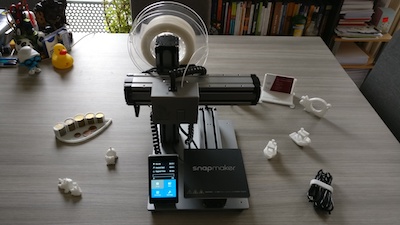
Historique
Comme mentionné dans l'introduction de cette section, l'impression 3D n'est pas une technologie récente. Dans le monde industriel, l'impression 3D existe depuis les années 1980. On attribue souvent sa paternité à Charles W. Hull, présenté à la figure 7a, ingénieur américain et actuellement Vice-Président exécutif et CTO de la société 3D Systems, par ailleurs récemment nommé au Prix de l'Inventeur Européen 2014, dans la catégorie inventeur non-européen.
En 1984, Charles Hull invente le procédé d'impression 3D par stéréolithographie. Son premier prototype d'imprimante 3D utilisait une résine synthétique et de la lumière ultra-violette pour la solidifier couche après couche. Le procédé de superposition de fines couches de matériau est toujours celui qui est utilisé aujourd'hui, malgré le développement de nouvelles techniques. C'est en 1986 que la première machine officiellement commercialisée par 3D Systems voit le jour. Suivra ensuite le premier modèle de série, la SLA-2502, destiné aux industriels désireux de produire des prototypes à la pièce, présenté à la figure 7b.
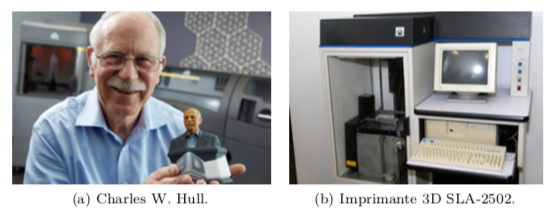
En parallèle à Charles Hull, d'autres inventeurs mettent au point des procédés d'impression similaires, basés sur le principe de l'impression additive. L'année 1989 est celle de l'invention de la Fuse Deposition Modelling (FDM), une technique d'impression par dépôt d'un matériel liquéfié, couche par couche, par une tête d'impression. C'est l'entreprise Stratasys, fondée un an plus tôt par Scott et Lisa Crump, qui est à l'origine de ce procédé, notamment utilisé pour les imprimantes 3D personnelles. Ce procédé est le sujet du chapitre 2.
Un autre procédé, mis au point en 1993 par le MIT et ensuite commercialisé par Z corporation en 1995, est la Three Dimensional Printing (3DP). Le principe ressemble fortement à celui de l'impression 2D : des gouttelettes de glue colorée sont déposées sur une fine couche de poudre composite, créant petit à petit un objet 3D avec la couleur désirée. La pièce est finalement chauffée et l'excédent de poudre aspiré.
Domaine médical
Un domaine dans lequel l'impression 3D a très vite évolué est celui de la médecine. En 1999, des scientifiques du Wake Forest Institute for Regenerative Medicine ont mis au point la première prothèse adaptable implantée dans le corps du patient. Cette grande première était une vessie adaptable, d'ailleurs enrobée de cellules du patient pour éviter tout rejet par son corps.
À partir de ce moment, l'évolution fut rapide et les prouesses médicales s'enchainèrent. Le premier rein imprimé en 3D et entièrement fonctionnel, capable de filtrer le sang et diluer l'urine, est greffé sur des animaux en 2002. Le premier membre prothétique a été conçu et imprimé en 2008. En 2010, Organovo voit le jour, la première bio-imprimante 3D capable d'imprimer un vaisseau sanguin fonctionnel. En 2011, une mandibule de mâchoire en titane est imprimée et implantée chez une patiente de 83 ans, ouvrant la porte de l'étude de la reconstruction de tissus osseux.
Mouvement open source
Un autre point clé qui a boosté l'impression 3D est la rencontre avec le mouvement de l'open source en 2005. Le Dr Adrian Bowyer, de l'Université de Bath en Angleterre, a mis au point un modèle d'imprimante 3D capable d'imprimer des pièces utiles à son propre fonctionnement. Le projet RepRap (Replication Rapid prototyper) vise à mettre à disposition les modèles 3D de différentes pièces constituant une imprimante, librement, en suivant la philosophie de l'open source. La figure 8 montre plusieurs modèles de ces imprimantes capables de s'imprimer elles-mêmes, du moins en grande partie. Ce projet ouvre l'opportunité pour un possesseur d'imprimante de créer d'autres machines pour ses proches et d'ainsi répandre la technologie de l'impression 3D.
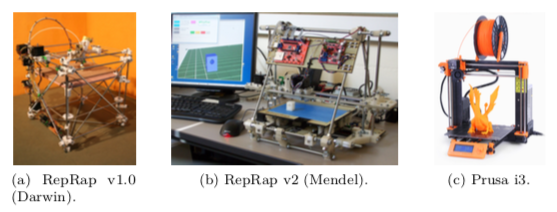
En 2008 le projet RepRap réussi son pari et abouti donc. Alors que les premières imprimantes capables de se répliquer sortent, l'entreprise ShapeWays voit le jour. Cette dernière propose un service d'impression 3D à la demande en permettant à ses clients, designers, architectes et ingénieurs, de créer des plans de manière conjointe, de les partager avec la communauté et enfin de les faire imprimer à un prix abordable.
Enfin, l'entreprise MakerBot Industries, fondée en 2009 par Bre Pettis à Brooklyn, s'appuie sur le projet RepRap pour concevoir une imprimante destinée aux particuliers, distribuée sous la forme d'un kit DIY et vendue à un prix abordable. Elle produira notamment le Makerbot Cupcake CNL en 2009, le Thing-O-Metic en 2010 ainsi que la série des Replicator à partir de 2012.
Industrie de l'impression 3D
Aujourd'hui, l'industrie de l'impression 3D explose, et atteint également le monde des particuliers. En effet, plus de 278000 imprimantes domestiques ont été vendues en 2015. La croissance de cette industrie, initialement horizontale, est passée à une tendance plutôt verticale de 2010 à 2015, et a dépassé les €4.8 milliards. Cette croissance est illustrée par la figure 9 basée sur les données publiées dans un rapport publié par Wohlers Associates.
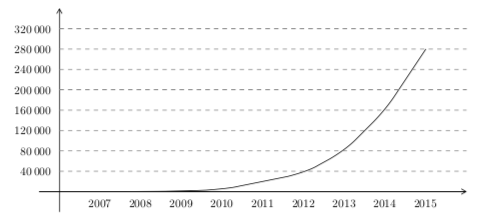
Les études et analyses récentes tendent à montrer que ce marché est en très bonne santé et que cette industrie devrait continuer à croitre. Le marché grand public explose et de plus en plus d'imprimantes « bon marché » voient le jour. Des prédictions, reprises dans un rapport de la Commission Européenne de janvier 2017, annoncent que l'industrie de l'impression 3D pourraient atteindre €9.64 milliards d'ici 2021.
Une autre étude, menée par Sculpteo en 2017, permet de mieux comprendre cette industrie. Cette dernière rassemble et analyse des données collectées auprès de pas loin de 1000 personnes provenant de 62 pays et couvre à la fois des consommateurs et des industriels. Voici différents éléments clés que l'on peut retenir de cette étude :
- La technologie de l'impression 3D est principalement utilisée pour accélérer le développement de nouveaux produits (28%) et produire des objets personnalisés en série limitée (16%). Parmi les principaux types d'objets produits, on retrouve les prototypes (34%) et les proof of concept (23%). Ceci est en claire corrélation avec le fait que ces technologies sont principalement utilisées dans le département R&D (62%) et le département design (53%) des entreprises.
- Concernant le type de matériau utilisé, on retrouve principalement le plastique (88%), les résines (35%) et le métal (28%). Les trois technologies majeures d'impression sont le Fuse Deposition Modelling (36%), le Selective Laser Sintering (33%) et la Stereolithography (25%). Enfin, parmi les techniques de finition, on retrouve essentiellement le polissage (33%) et la peinture (19%).
Révolution de la fabrication
L'impression 3D est réellement une révolution de la fabrication personnelle. Grâce à cette dernière, n'importe qui peut maintenant avoir une véritable « usine personnelle » sur son bureau et à un prix abordable.
On assiste ainsi à un véritable déplacement d'une série d'activités des usines vers des plus petits magasins. Il devient, par exemple, tout à fait pensable, et ça se fait, d'usiner et de fabriquer des objets dans des zones rurales et urbaines. De plus, il n'est plus du tout nécessaire de produire un objet en masse, on peut se limiter à un seul exemplaire.
Cette révolution rend le prototypage plus facile et accessible, n'importe qui peut s'essayer à concrétiser ses rêves les plus fous. Le prototypage est rendu plus abordable à moindres couts, ouvrant la porte à des méthodes de développement plus agiles.
Fabrication agile
Les méthodes agiles sont très utilisées dans le cadre de projets de développement logiciel. Elles sont aujourd'hui un choix privilégié pour les entreprises et ont certainement contribué à la croissance rapide de l'industrie du software ces dernières années. Ces méthodes impliquent au maximum le client et permettent une plus grande réactivité à ses demandes. De plus, elles reposent sur un cycle itératif court qui se concentre notamment sur la production régulière d'une solution, pas encore forcément complète et finie, mais fonctionnelle et démontrable au client. Ce dernier peut par conséquent rapidement fournir du feedback, qui permettra aux développeurs d'ajuster le tir et les prendre en compte pour l'itération suivante.
Aujourd'hui, ce type de méthode peut s'appliquer à d'autres domaines. La fabrication agile permet d'éliminer les désavantages des systèmes de contrôle en cascade que l'on retrouve dans les méthodes plus traditionnelles. Elle permet également, et c'est beaucoup plus motivant pour les Makers et les clients, de diminuer le temps nécessaire pour terminer le produit demandé. Le fait que l'imprimante 3D est aujourd'hui devenue plus abordable a complètement ouvert les portes de la fabrication agile.
La figure 10 montre les principales étapes d'un cycle d'une fabrication suivant une méthodologie agile. On y retrouve les mêmes phases que pour le développement logiciel, mais adaptées dans le contexte de la fabrication. Après établissement des exigences, le développeur passe au design puis à la construction de l'objet à fabriquer. Celui-ci est ensuite testé, pour s'assurer qu'il a un niveau de qualité suffisant et pour vérifier qu'il satisfait au client. Suite à ces tests, soit une version du produit est délivrée (OK), soit un nouveau cycle démarre après avoir établi les évolutions ou ajustements à faire (KO).
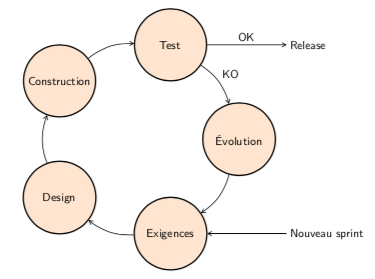
En suivant une méthode agile de fabrication, le concepteur d'un nouvel objet va procéder par itérations courtes. Au terme de chaque cycle, il aura un prototype à présenter au client pour récolter son feedback, permettant à l'objet de s'améliorer itération après itération. L'impression 3D accessible au plus grand nombre facilite évidemment ce type de développement. Les autres techniques de fabrication digitale sont également souvent disponibles, par le biais de fablabs locaux.